Epoxy coating acts as a protective shield that goes right over rough flooring. It can withstand impacts, shocks, and heavy weight without chipping or breaking down.
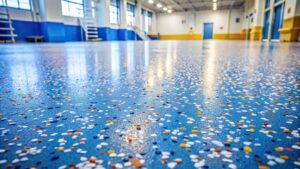
Adding graphene derivatives to an epoxy resin increases corrosion protection. In a study, rGO was silanized with APTES or GPTMS and added to an epoxy formulation that protected steel from corrosion.
Epoxy coatings are a great choice for floors that will be exposed to moisture, spills, or high foot traffic. Their anti-slip properties help prevent accidents, creating a safer work environment for employees and reducing downtime due to injuries. The textured surface of epoxy coatings improves traction and reduces the risk of slippage, particularly in wet conditions. Additionally, some epoxy floor coatings include aggregate to enhance traction.
Non-slip epoxy coatings are available in a variety of textures to suit specific application needs. For example, a coarser texture is better suited for a warehouse floor than a fine texture. It also provides a more durable surface that resists abrasion and wear. Alternatively, you can opt for a softer texture that is more comfortable to walk on.
The texture of a non-slip epoxy coating can be enhanced further by adding abrasive aggregate, such as crushed glass or aluminum oxide. These materials are added to the base coat before the topcoat is applied. You can also find grit additives that are designed to be mixed into an epoxy coating or broadcasted on the surface.
Aside from slip resistance, a non-slip epoxy coating can offer other protection against environmental contaminants. Coatings that are exposed to harsh chemicals, such as acids or dyes, can be damaged over time by the abrasive elements in these substances. Coatings with an anti-corrosive property can prevent the formation of flash rust on steel surfaces.
Many people assume that they can apply an epoxy coating and immediately start using the area. However, the reality is that a lack of surface preparation is responsible for up to 80% of all cases where an epoxy coating fails prematurely. To avoid this issue, it’s important to ensure the appropriate environmental conditions are met and that the right type of abrasive media is used for blasting the surface.
Water Resistant
Epoxy coatings have good water resistance properties, allowing them to form an airtight seal that prevents the infiltration of water. The water resistance of epoxy depends on the type of epoxy selected, as well as the preparation and curing processes. The substrate’s condition also impacts the coating’s water resistance. Ensure proper cleaning, degreasing, and roughening prior to coating to maximize adhesion and minimize potential entry points for moisture. Moreover, maintaining precise temperatures and humidity during curing will promote the best results.
Many people are interested in using epoxy to serve as a waterproof membrane on commercial, residential, or industrial projects. Epoxy waterproofing can be used on decks, concrete slabs, walkways, and other surfaces that are susceptible to high hydrostatic pressure, potential movement, or radon gas migration. However, it is important to remember that no epoxy offers absolute waterproofing and that dedicated waterproof membranes are still the best option for critical applications requiring high performance standards.
Various methods are available for enhancing epoxy coatings’ water resistance, including surface modification and nanofiller additions. One method involves grafting GO with a conductive polythiophene chain, which enhances corrosion resistance by promoting passivation film formation on steel surfaces. GO/PTh grafting was performed through in-situ polymerization, followed by a PTh-GO dispersion in acetone and subsequent mixing with an epoxy resin and curing agent. The resulting GO-PTH/epoxy coating was sprayed onto a sandblasted stainless steel plate, cured at room temperature and then at moderate temperatures, and subjected to a corrosive media test. The GO-PTH/epoxy samples presented the highest impedance values, indicating that GO significantly enhanced the epoxy’s corrosion protection potential due to its improved dispersion on epoxy and its ability to function as a physical barrier against water, oxygen, and other corrosive materials.
Durable
Epoxy is a strong and durable material, especially when properly applied. Proper maintenance practices are also essential to extend the life of epoxy coatings and maintain their high-performance properties. Regular cleaning, for example, can remove dirt and abrasive debris that can scratch the surface and reduce its durability.
Regularly sweeping and vacuuming can also help prevent contamination from chemicals or abrasive particles that could damage the epoxy resin or expose bare substrate. Proper storage and handling can also ensure that the epoxy does not become exposed to heat or moisture, which may affect its chemical resistance and dimensional stability.
In addition to their physical strength and longevity, epoxies are highly versatile and can be used for many applications. They are often used as adhesives or repair materials, especially for etched copper tracks on PCBs and as conductive joints between flexible conductive components and rigid grounding. They can also be formulated with moderate conductivity to allow them to carry low currents or signals.
Conductive epoxies can be modified with graphene or other semi-conducting materials to improve their conductivity and increase their use as protective coatings. For example, one study found that amino-functionalized regenerated cellulose (rGO) enhanced the corrosion resistance of an epoxy coating over mild steel. In this study, rGO was functionalized with APTES and GPTMS via the standard toluene route, and it was dispersed in acetone and mixed in an epoxy resin with a polyamide hardener before application onto the metal substrate and curing. Adding 2.5 wt% of P-AT-rGO significantly improved the corrosion resistance of the epoxy coating. This was attributed to the GO’s superior dispersibility in solvents and its ability to form non-covalent bonds with GR.
Chemical Resistant
Chemical resistance of a material refers to the ability of the material to resist degradation due to chemical attack. This damage can be caused by a number of things, including corrosion, oxidation, or other chemical reactions. Epoxy coatings can help protect a surface from these chemicals and provide abrasion resistance. For example, pipes transporting crude oil can be subjected to abrasion, which can cause cracks and leaks over time. Abrasion-resistant epoxy coatings can protect the surface of these pipes and help extend their lifespan.
The chemistry and network structure of an epoxy coating are significant factors in its chemical resistance properties. The resin, curing agent, and diluent all contribute to the overall network structure of the coating. The amount of crosslinking in the epoxy also impacts its resistance to specific chemicals. For example, a tighter network will have better resistance to swelling and diffusion of chemicals.
Conductive epoxies are often used in the electronics industry as a coating for etched copper traces on printed circuit boards, and as repair pastes to bridge conductive sections of broken PCBs. Conductivity of an epoxy coating can be increased by adding conductive fillers, such as carbon fiber or fullerenes. This enables the epoxy to carry low currents and signals through the substrate, which can be helpful in electronic applications.
Recently, an amino functionalized GO (fGO) has been added to an epoxy-based system to improve its abrasion and corrosion resistance properties. This fGO was silanized with 3-(glycidoxypropyl) trimethoxysilane (GPTMS) or 2-(aminopropyl) triethoxysilane (APTES), and then dispersed in a polyamide hardener and mixed into the epoxy. The abrasion and corrosion resistance of the epoxy coating with this additive was compared to a standard epoxy coating using a Brookfield single-cylinder rotational viscometer and TECHNE gelation timer model FGT 6. The results showed that fGO had double the adhesion and water contact angle as the neat epoxy.
Shock Resistant
Thermal shock resistance is an important property for potting and coating applications. It allows the epoxy to withstand high temperatures, while still remaining flexible enough for use on surfaces that will experience a lot of movement and stress. A good thermal shock resistant epoxy will also have excellent shear and peel strength, which will help to prevent damage or failure of the substrate being coated.
A number of different epoxy formulations have been developed to meet specific requirements for a variety of projects. When choosing the right epoxy for your project, consider the type of surface you will be coating, the environmental conditions, and your budget. It is also important to adhere to the manufacturer’s instructions regarding curing times and temperatures, as overheating or stressing part-cured epoxy can decrease its durability.
One method of increasing the chemical resistance of an epoxy coating is to add a grafted cellulose nanofiller. This is a great way to improve the flexibility and durability of an epoxy-based product, as well as to reduce the amount of toxic chemicals used in the formulation.
Other methods of improving the corrosion resistance of an epoxy-based product include adding graphene or other carbon-based nanomaterials to the formulation. GO has been silanized with APTES and GPTMS to create a graphene-modified epoxy resin, which has been shown to be highly effective at protecting steel against corrosion.
Many industrial and household items are treated with epoxy powder coating to protect them from corrosion, wear and tear, and harsh environments. This includes electrical components such as wires and cables, which are constantly exposed to heat and moisture. It’s also common to see epoxy coating on construction items, such as rebar and steel poles, power tools, and hand tools, which are often subjected to extreme heat and stress.